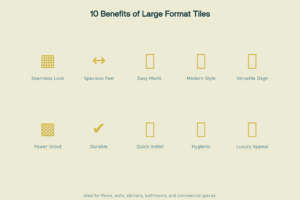
Future Stiles is a relatively new player in the tile industry, but it has quickly gained recognition for its innovative and modern designs. The brand focuses on merging cutting-edge technology with artistic craftsmanship to create unique and visually appealing tiles.
There are different applications in which refractory bricks serve as main components, known for their ability to withstand very high temperatures. From steel making to ceramics, they are used by a wide range of industries due to their thermally resistant and structurally strong nature that allows them to be able hold up under intense heat during production.
Refractory bricks or firebricks, as they are also referred to, are purpose-built ceramic products created specifically to operate at elevated temperatures and counteract harsh surroundings. These materials possess the highest thermal stability, chemical resistance and mechanical strength among other ordinary bricks hence absolutely needed in high temperature industrial installations.
The composition is one major way of classifying different types of refractory bricks. Some common types include;
Among the most commonly used refractory bricks include Fireclay Bricks. They are made from a naturally occurring material that is rich in alumina and silica called fireclay. Thermal shock resistance is excellent while tolerance of high temperatures is another characteristic of fire clay brick. They can be found in furnaces, kilns and even chimneys.
High alumina bricks contain more alumina (Al2O3) than fireclay bricks, so they are known as such because of this fact. As the result they have better resistance against high temperatures and slag corrosion. They are chosen when working in blast furnaces, steel ladles or cement kilns since these constructions endure very hot atmosphere along with corrosive surrounding conditions
Silica bricks constitute mainly silica (SiO2). These have the unique property of retaining their shape at temperatures up to 1650°C (3002°F). Silica bricks are widely employed in glass melting furnaces and coke ovens because of their very good thermal stability and resistance to acid slags.
Magnesia bricks consist of magnetite (MgCO3), with a high proportion of magnesium oxide (MgO). They are best known for being tolerant to alkaline slags and capable of withstanding high temperatures. They are commonly used in steelmaking furnaces, especially in converters and electric arc furnaces.
Magnesia bricks consist of magnetite (MgCO3), which has a high concentration of magnesium oxide content (MgO) . These bricks have excellent resistance against basic slags and the ability to withstand high temperatures. In addition, they are often applied as linings in converters and electric arc furnaces that are used by steel makers.
Zirconia brick is made from zirconium dioxide /ZrO2/. It is characterized by its high melting point, exceptional resistance to thermal shock, as well as chemical attack. In extreme temperature conditions like nuclear reactors or glass melting tank, Zirconia brick is usually preferred.
Zirconia brick is made of zirconium dioxide. It has a high melting point, excellent resistance to thermal shock and chemical attack. In extreme temperature conditions like nuclear reactors or glass melting tank, Zirconia brick is usually preferred.
There are many uses of refractory bricks in various industries due to their distinctive properties. Some of the key uses include:
Refractory bricks are indispensable in the steel and iron industry since they are used in the fabrication of blast furnaces, converters as well as ladles. These structures work at very high temperatures and therefore come into contact with corrosive slags and molten metal. They have adequate thermal resistance and structural stability.
The cement industry heavily depends on refractory bricks for lining its rotary kilns and coolers. The kilns operate at a very high temperature converting raw materials into clinker. Thus, refractory bricks protect them from thermal damage, chemical impact; thus ensuring long life and efficiency of these kilns.
Refractory bricks are important in the glass industry where they are employed in making glass melting furnaces. High temperatures need materials that can withstand thermal shock and chemical corrosion that occurs due to the need to melt glasses.
Kilns used to fire ceramics and pottery in the ceramics and pottery industry utilize refractory bricks. In order for these kilns to produce high-quality ceramics, they must be at a high constant temperature. Because of their thermal stability and resistance to thermal shock, fireclay bricks and high alumina bricks are often used in these applications.
In non-ferrous metal industry furnaces smelting metals such as aluminum, copper, lead, etc., refractory bricks become useful. These furnaces work at high temperatures with corrosive slags. Due to the basic slags resistant nature mantle brick magnesia brick and chromite brick are commonly employed here which can withstand heat effects.
Particularly boilers and incinerators in power generation plants use refractory bricks. Such structures work under high temperatures conditions hence they require materials that can resist both chemical attack and thermal stress. That’s why in these cases either fireclay or high alumina bricks are usually preferred.
The petrochemical industry utilizes refractory bricks in reactors, reformers, and other units that have a high-temperature process path. For this reason, there is a need for materials capable of resisting thermal cycling and chemical corrosion within these surroundings. Refractory is what saves them from frequent replacements hence ensuring safe operations on efficiency grounds.
Kilns are a basic part of many industrial processes, especially in the fields of ceramics, cement and glass. The performance and efficiency of kilns greatly depend on the quality of refractory bricks used in their building.
Refractory bricks are an integral part of several high temperature applications due to their necessary thermal resistance
Chat Now